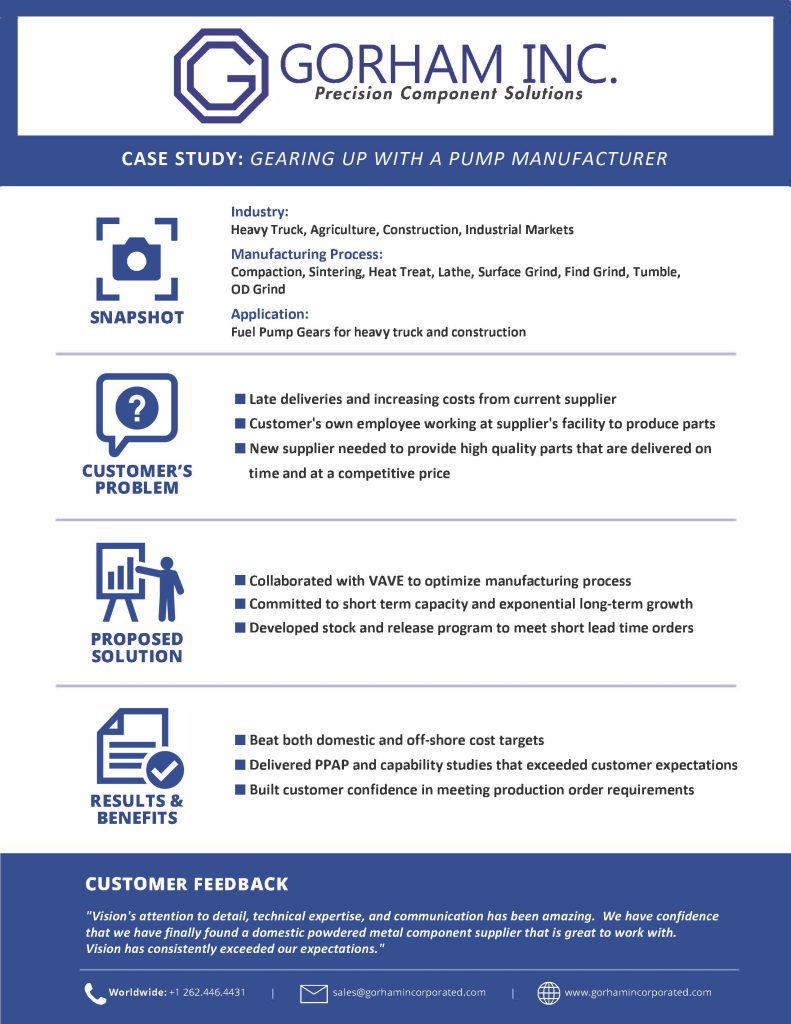
Case Study #5 – Powdered Metal
February 14th, 2023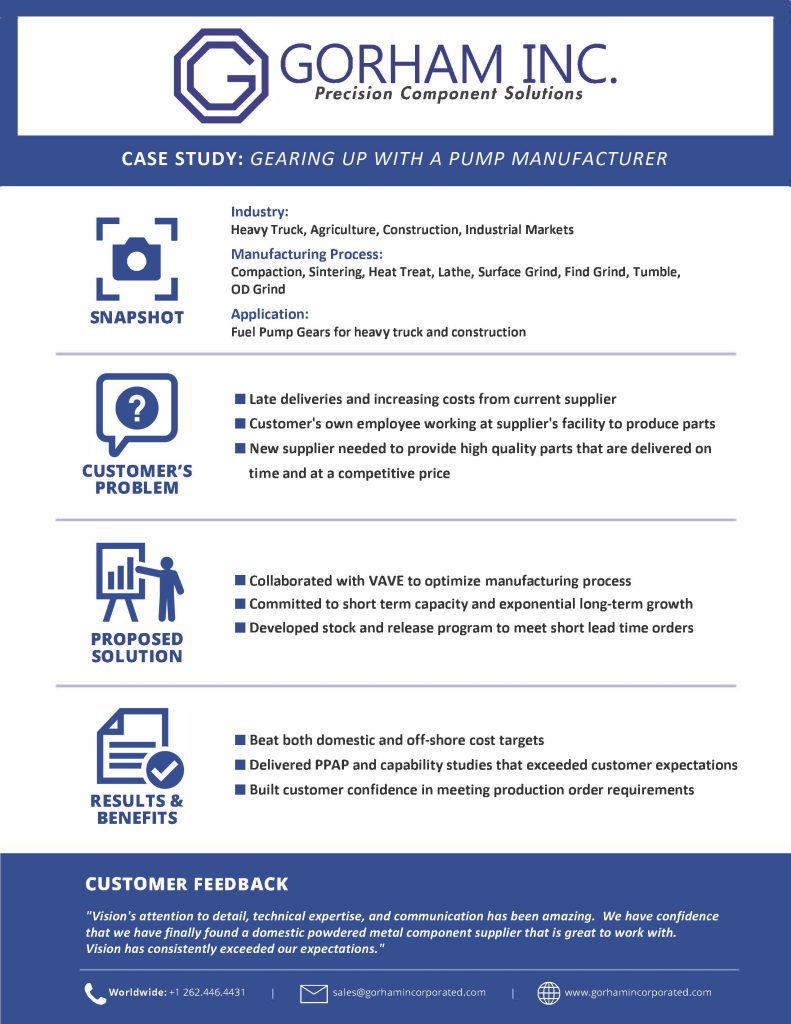
Tags: Powder Metal, powdered metal, sintered metal, sintering
Posted in Powder Metal Parts | No Comments »
Your Source for Powder Metal Components
January 25th, 2022Are you looking for a new application, or have the need to improve upon an application that already exists? We can offer exclusive engineering assistance for conversions of other process designed components to high quality Powder Metal Components with significant cost savings and minimal waste during production.
Many Material Options Available Step one: Choose the metal powder material which will produce the component properties that meet or exceed the customer’s expectations in their application. Options include iron, bronze, brass, stainless steel, magnetic blends, and more. |
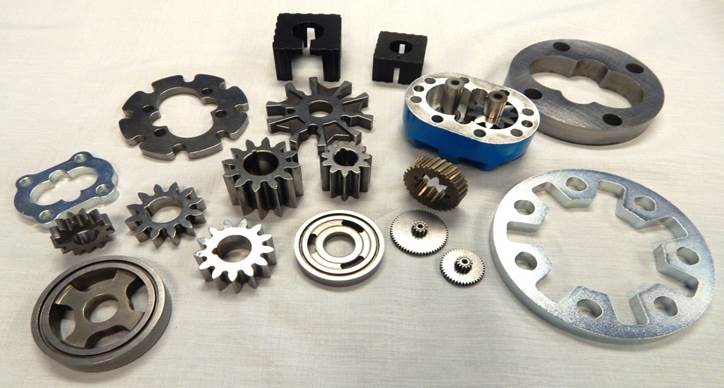
Tags: Powder Metal, powdered metal, sintered metal
Posted in Powder Metal Parts | No Comments »
Powder Metal Components
February 18th, 2021Are you interested in SIGNIFICANT cost savings by converting a machined component to powder metal? Contact us today to see if we can unlock some savings for you.
The powder metal (also called sintered metal) process consists of three basic steps; powder blending, die compaction and sintering. Dry powder is pressed into a mold that produces precise parts and then goes through a sintering process to create a stable part. This process is best suited for smaller complex parts that require tight tolerances.
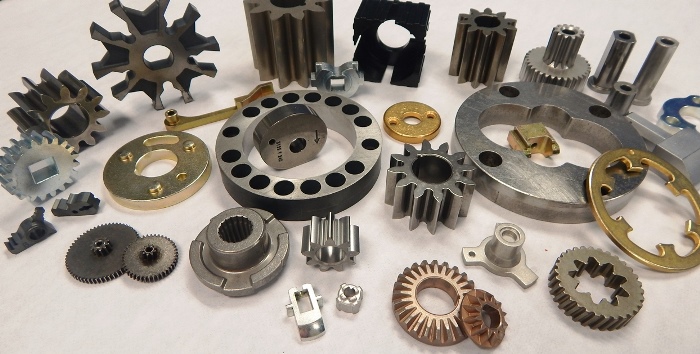
Tags: die compaction, powder blending, Powder Metal, Powder Metal Components, powdered metal, sintered metal, sintering
Posted in Powder Metal Parts | No Comments »
Your Local Source for Powder Metal Parts
March 17th, 2017Why Powder Metal?
Significant Cost Savings, Complex and Unique Shapes, Minimal to No Waste in Production, Low to High Volume Runs, High Material Strength, Part to Part Consistency, Cost Efficient, Lower Tooling Cost, No Tool Maintenance, Dimensional Control, Elimination of Costly Cutting , Varied Surface Finishes, Tight Tolerances
Materials Used:
High Strength Steel, Stainless Steel, Bronze, Brass, Soft Magnetics
Tags: brass, bronze, complex shapes, consistency, cost efficient, cost savings, dimensional control, high strength, illinois, low tooling cost, magnetics, metal parts, minimal waste, Powder Metal, Steel, surface finishes, Tight Tolerances, wisconsin
Posted in Powder Metal Parts | No Comments »
Highly Engineered Powder Metal Parts
June 6th, 2016Why Powdered Metals?
- Significant cost savings.
- Create complex or unique shapes.
- No or minimal waste during production.
- High quality finished products.
- Material strength.
Powder metal parts are a perfect fit for a variety of applications in many different industries. The efficient, high-volume production is a great way to cut your manufacturing costs without sacrificing quality. Making quality components from powdered metal produces cost savings by reducing, or even eliminating, expensive machining and material scrap.
We offer exclusive engineering assistance for conversions of other process designed components to high quality, cost effective, Powder Metal Components. We have many material options including Alloy Steels, Stainless Steels, and Brass.
We offer Fine Pitch Precision Gears for your Motion Control Applications in Gear Motors, Gear Actuators, Gear Reduction, and Gear Drives; Specialty Helical Gears; Carbon Steel and Alloy Steel Pump Gears for Low and High Pressure Pumps; Components for your Knob Locks, Lever Locks, Mortise Locks, Panic Bars, Padlocks, and more!
Tags: cost savings, engineered, gears, high quality, illinois, lock components, material strength, multi-level structural components, Powder Metal, powdered metal, wisconsin
Posted in Powder Metal Parts | No Comments »